
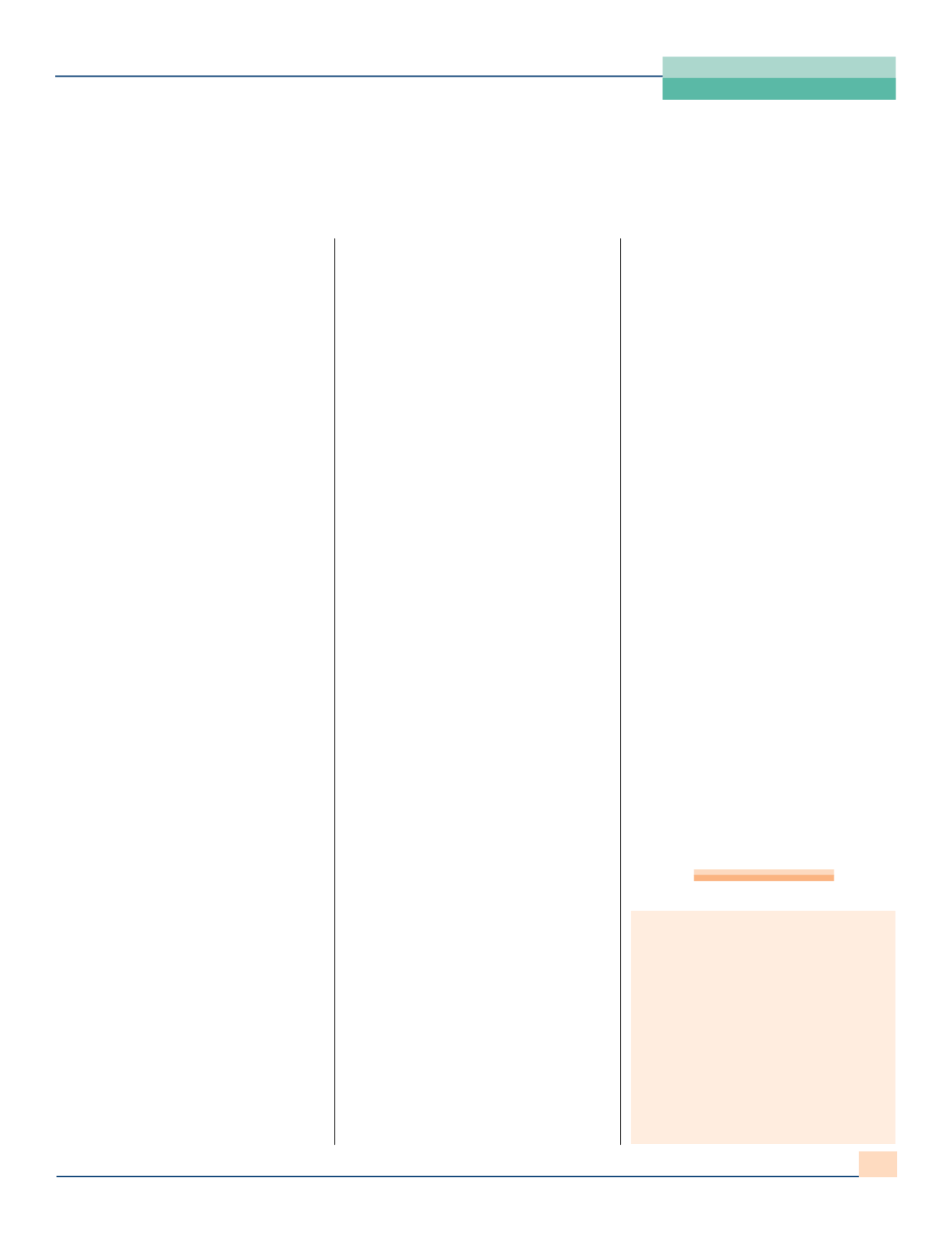
WORLD-GENERATION NOVEMBER/DECEMBER 2016
17
PERSPECTIVE
SEVILLE,SPAIN - Heineken is the
number one brewer in Europe and number
three brewer in the world with operations
in 71 countries with an annual beer
production of 181 million hectoliters in
one hundred and sixty-five breweries with
seventy-six thousand employees.
Sustainability has been a core operating
principal for Heineken for 150 years.
In 2010, as part of its ongoing
commitment to sustainability, Heineken
introduced a comprehensive 10-year
sustainability plan that affected all aspects
of the operations.
For the Seville brewery this meant
reducing water consumption by 25% and
reducing CO2 emissions by 40% based on
their 2008 levels.
In 2012 when the brewery started
approaching its technological limit, the
brewery realized it was going to need
another tool if it was going to meet the
2020 targets. We knew we were close to
the technological limit; it was clear that we
needed an energy and water monitoring
and reporting system if we wanted to keep
moving forward because we spent 80% of
our time collecting information and 20%
analyzing it when it should be the
opposite.
The PI System solution is very flexible
and is accessible for everyone.
SOLUTION
In 2012, Heineken España installed
the PI System at the brewery in Seville.
The brewery also decided that Asset
Framework (AF) was going to be a core
part of the solution, as we have many silos,
non-intuitive tag names and a lot of
equipment across the different processes.
AF CAPABILITIES
In addition to organizing data and
making it more user friendly, AF has
given the brewery increased calculation
capabilities.
Now, when machines are defined in
AF, the primary sustainability attributes
(electricity, water, and thermal energy
consumption) are also defined. This
means that sustainability data is available
for each asset and as roll up data across
divisions, in real-time as absolute values,
in per shift, per day, and per week totals,
and in weekly and monthly ratios that
show the amount of water, electricity, and
thermal energy consumed per hectoliters
of beer produced.
AF has also allowed the brewery to
group their data and sustainability metrics
based on the roles of the users.
The end result is users see data for
their areas of responsibility in a structure
they understand.
PI SYSTEM
The Seville brewery has seen several
benefits from their PI System deployment.
The PI System has made information
easier to access. We spend 10% of our time
collecting data and just enjoy analyzing
information the rest of the time.
It’s totally the opposite of a few years
ago.
The PI System has also improved data
quality. In the old software we were
missing efficiency data, ratio data,
historical values, we needed more
flexibility in graphs. Now we can check in
real-time efficiency, power, pressure, and
flow and see efficiency values for the last
24-hours, last week and last month.
Since the PI System is easy to use, the
Seville brewery has been able to extend
their data to new users. Each department
has to own their own consumption. With
the PI System, they develop screens and
control consaumption in real-time.
With improved data and the ability to
view sustainability metrics in real-time,
the Seville brewery can view real-time
operations against both yearly
sustainability targets and historical
process levels and make dynamic process
adjustments.
As a next phase in its implementation,
the brewery is planning to switch from
fixed yearly targets to dynamically
recalculating yearly targets that adjust
based on real-time production and current
climate conditions.
PI DATALINK AND PI PROCESSBOOK
In addition to improving real-time
information access, we use PI DataLink
and PI ProcessBook playback to analyze
historical problems. Using playback we
can analyze second by second what
happened in the past.
ABOUTTHE AUTHOR
Consuelo Carmona Miura is an
Industrial Engineer specializing in
Organization and Production; and has a
Master’s Degree in Thermal Energy
Systems, Energy Savings and Efficiency.
Miura joined Heineken in 2008, working
in TPM (Total Productive Management)
for two years.
For the last three years, Miura has
worked as a Utilities Manager and Energy
Champion and in September begins her
role as Electricity European Project Lead.
LEVERAGING DATA FOR SUSTAINABILITY
BY CONSUELO CARMONA MIURA,HEINEKEN ENERGY PROJECT HEAD
NEXT ISSUE
Class of 2017
February/March 2017
Closing February 28, 2017